ABS-CBN Official Website | Leading Entertainment and News Network | ABS-CBN
ADVERTISEMENT
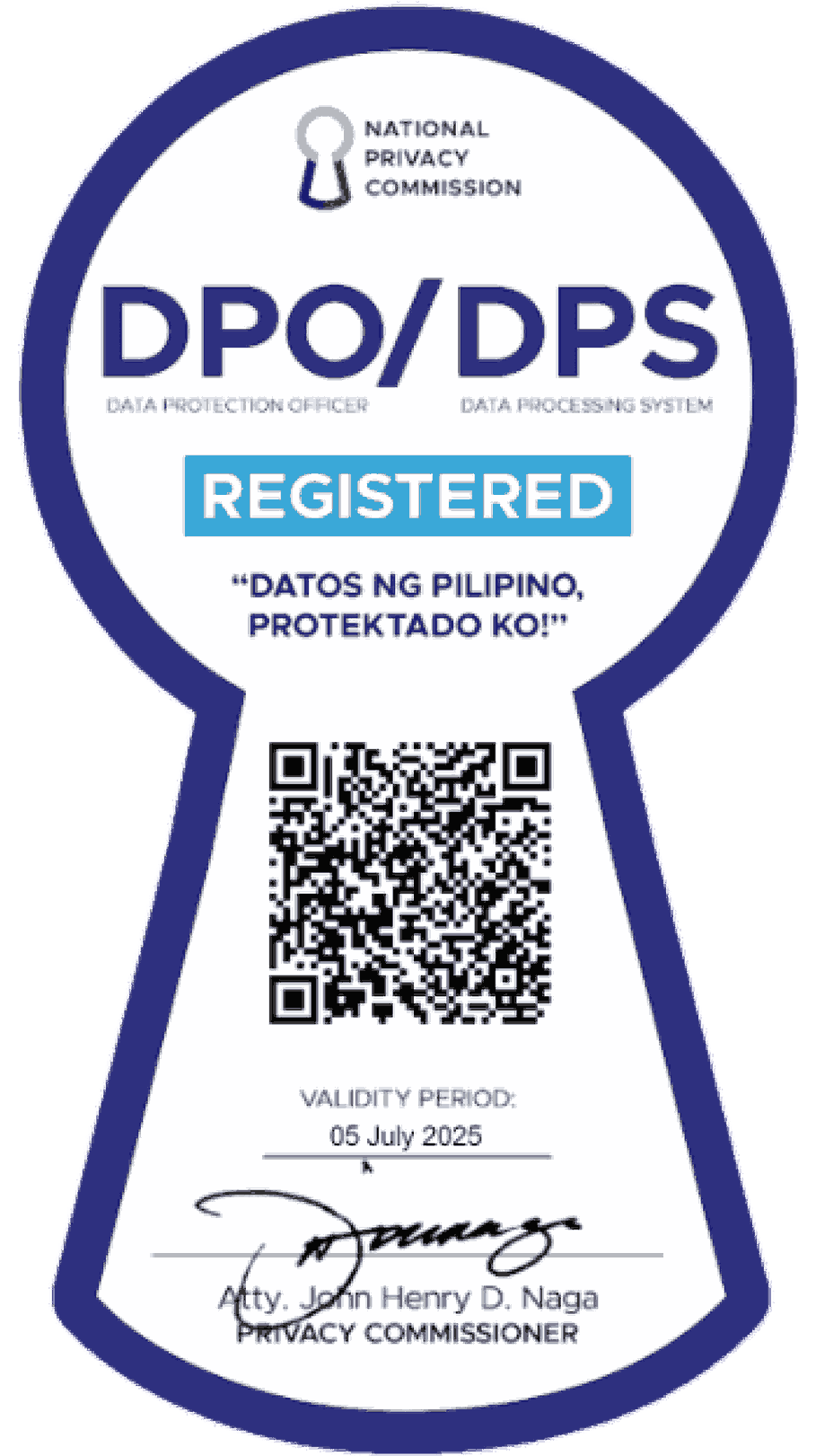
Welcome, Kapamilya! We use cookies to improve your browsing experience. Continuing to use this site means you agree to our use of cookies. Tell me more!
LIVE UPDATES
LIVE UPDATES
Nation
'The voice of God': Filipinos wrestle with death of Pope Francis
'The voice of God': Filipinos wrestle with death of Pope Francis
Pope Francis, who appointed three of the 10 Filipino cardinals in Church history, visited the Philippines only once, when he led a mass for survivors of Super Typhoon Yolanda.
Celebrities
Editors' Picks
Editors' Picks
ADVERTISEMENT
Latest Videos
Latest Videos
ADVERTISEMENT
Latest News
Latest News
ADVERTISEMENT
ADVERTISEMENT
ADVERTISEMENT