ABS-CBN Official Website | Leading Entertainment and News Network | ABS-CBN
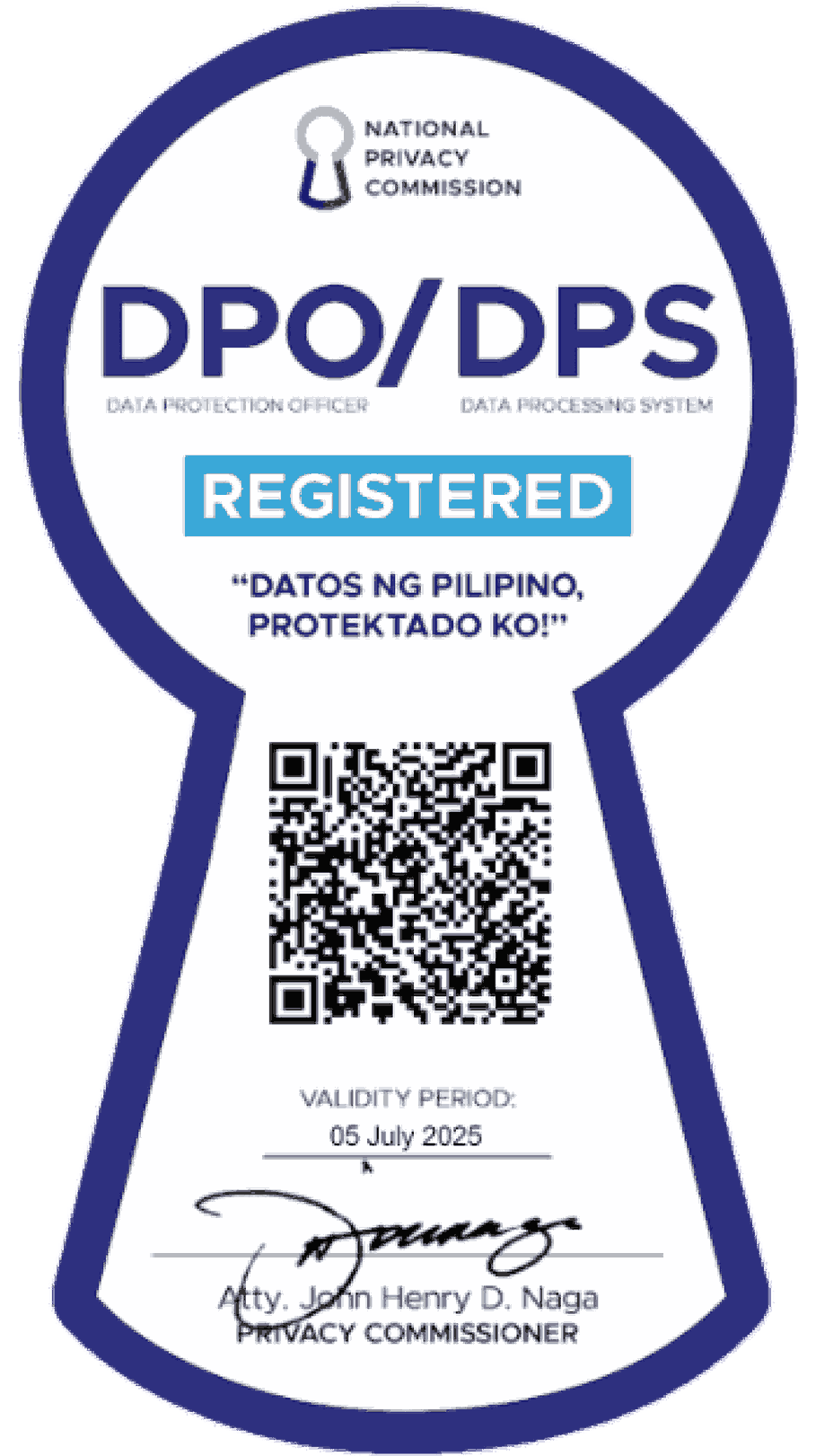
Welcome, Kapamilya! We use cookies to improve your browsing experience. Continuing to use this site means you agree to our use of cookies. Tell me more!
Editors' Picks
Editors' Picks
ADVERTISEMENT
Latest Videos
Latest Videos
ADVERTISEMENT
Latest News
Latest News
ADVERTISEMENT
ADVERTISEMENT
ADVERTISEMENT