ABS-CBN Official Website | Leading Entertainment and News Network | ABS-CBN
ADVERTISEMENT
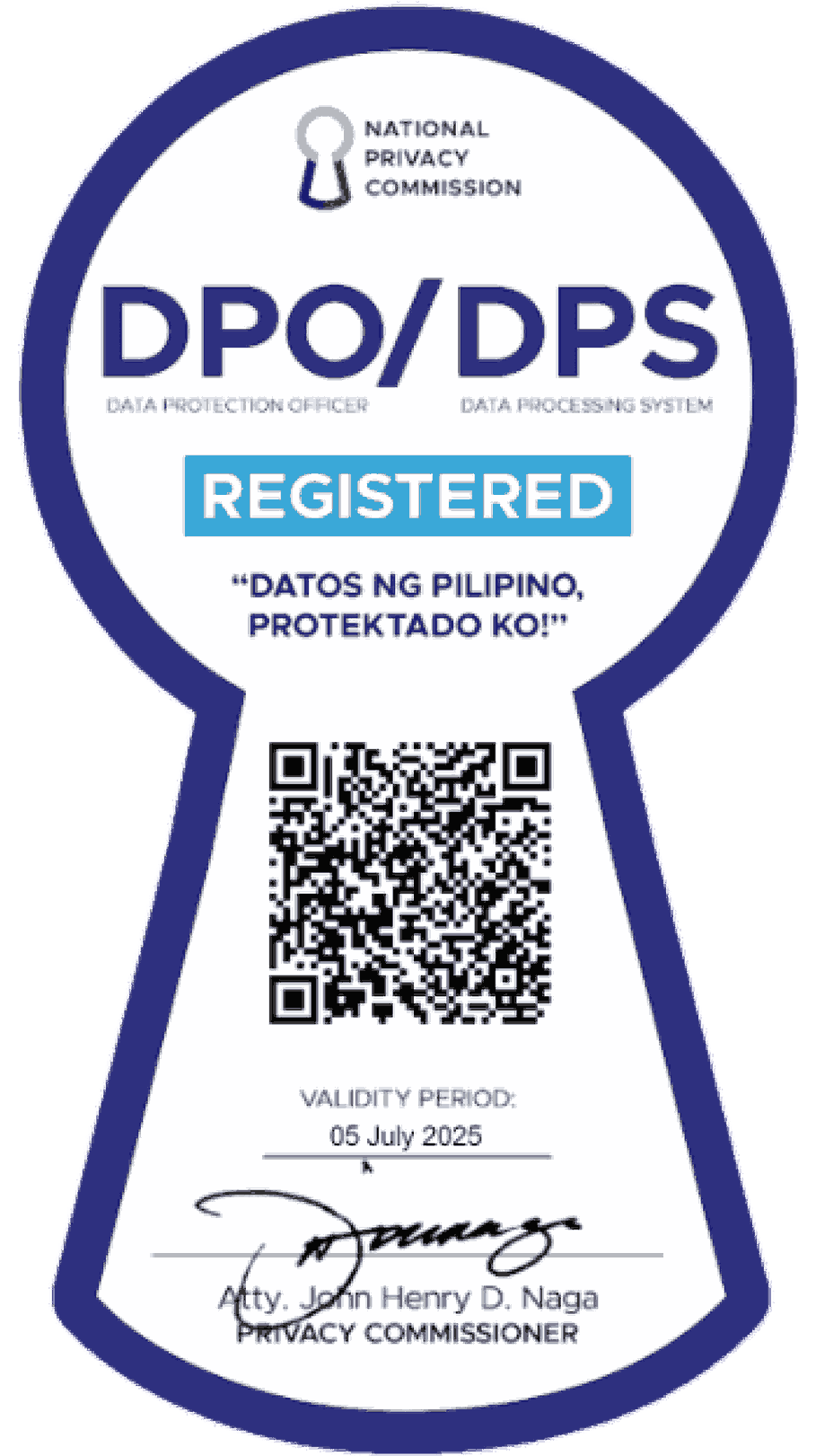
Welcome, Kapamilya! We use cookies to improve your browsing experience. Continuing to use this site means you agree to our use of cookies. Tell me more!
Nation
Assault complaint vs Sara Duterte junked
3 hours ago
Nation
Movies & Series
Nation
Nation
Comelec, TikTok ink deal for 2025 polls
3 hours ago
Other Sports
Editors' Picks
Editors' Picks
ADVERTISEMENT
Latest Videos
Latest Videos
ADVERTISEMENT
Latest News
Latest News
ADVERTISEMENT
ADVERTISEMENT